
This is in case the fault is in the mill. One thing you could try first is to swap over your wires U1 and U2 to see if is the same actual motor direction that is slow to start or the same direction push button. (As I believe this is the start capacitor.) These tests should help to confirm if my understanding of the motor's internal wiring is correct. Z1 to V2 I expext this to give a low resistance reading when the meter is first connected but the reading will slowly increase to a high value as the capacitors charge.Ĭan you confirm that capacitor B is the one with the largest value. With the metal straps removed and no external connections to the motor do the following resistance checks and report the results. Either one should start the motor.) If the motor runs correctly in both directions then do the following tests to see if I have correctly understood the motor's internal wiring. The direction buttons will not effect the direction. (You can use the U1 and U2 wires from the mill as the supply for this test but make sure you have made the ends of the Z1 and Z2 wires safe as these will also be live. Repeat the test with the straps in the positions for the anticlockwise direction. Re fit the metal straps in the position for the clockwise direction and connect the supply to U1 and U2 (As in the second picture of your first post) Check that the motor starts and runs correctly in that direction. Try the motor without the control gear in the mill.
FORWARD AND REVERSE MOTOR STARTER DIAGRAM SOFTWARE
s as the forum software removed the spaces so the diagram did not make sense. The UK time of this post is about 09:11 so you have an idea of the time difference.Įdit. If this is the case then the way I suggesred connecting the motor should be correct. If it is wired how I think it is then lamps 1 and 2 will be lit in both directions. The lamps that light in both directions are the ones connected between the wires for a winding. In the other direction only two lamps will light.

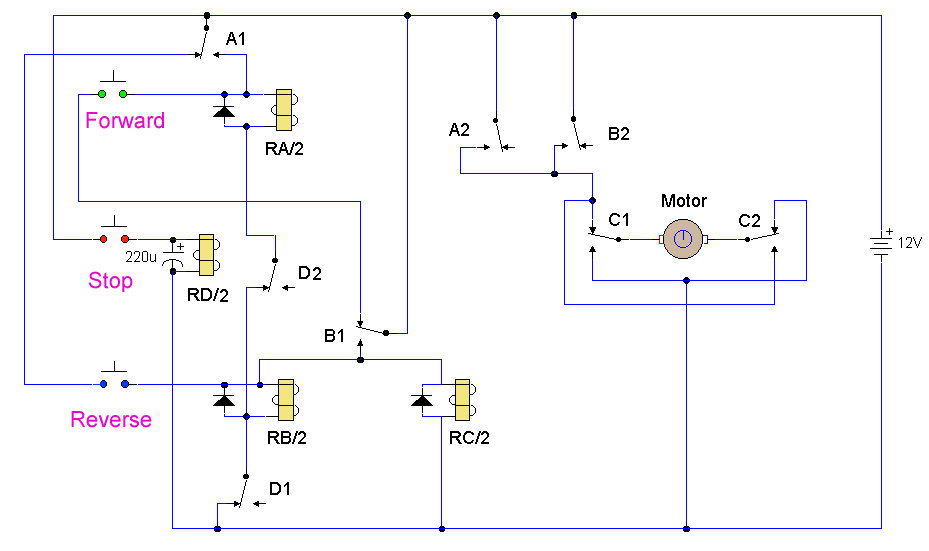
In one direction all four lamps will light. That would be one way but it may be quicker to connect the four wires to four lamps (Old filiment type bulbs. If forward and reverse are the wrong way round swap over the wires U1 and U2. If you post a schematic we should be able to see if this is the case. There may already be thermal overcurrent protection in the control gear.
FORWARD AND REVERSE MOTOR STARTER DIAGRAM SERIES
To use it to disconnect both windings you would need to run two more wires back to the control box and connect it in series with the live feed to the forward and reverse contactors. This will now only disconnect the main winding. Connect the wire marked Z2 to terminal Z2. Connect the wire labeled Z1 to terminal V1. Connect the wire labled U2 to terminal V2. Connect the wire labled U1 to terminal U1. Remove the two metal straps but put the wires back on the same terminals. If you get these reading then the following instructions should do what you want.
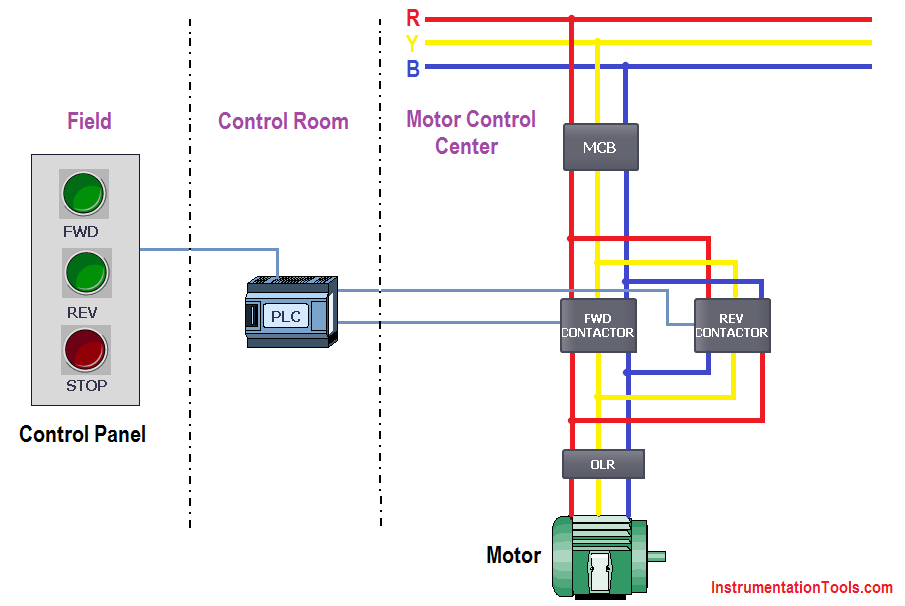
There should be a very high resistance (Greater than 50 Meg ohms.) between a terminal that had a red wire and a terminal that had a black wire. You should also measure a low resistance between the teminals that had the black wires connected to them.
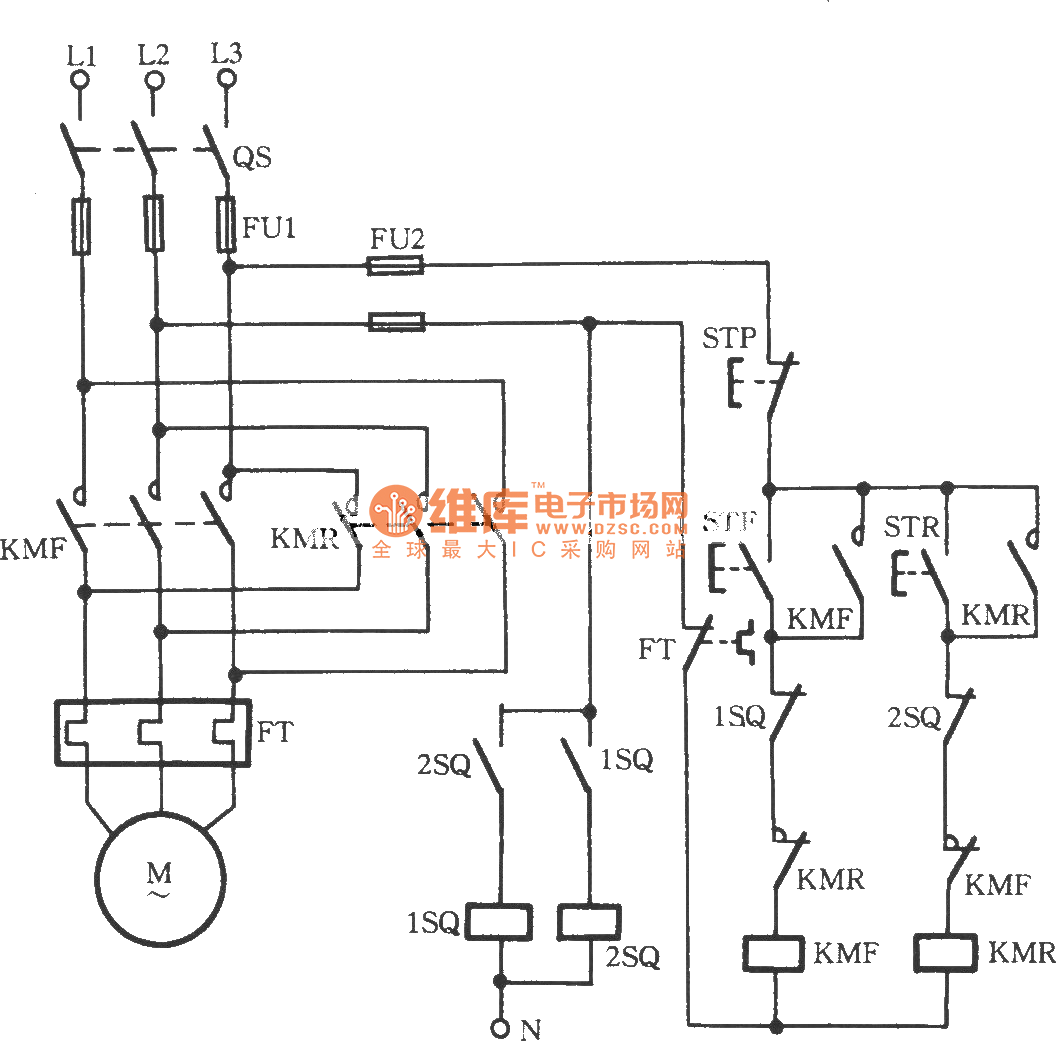
If I am right then on the old motor you should measure a low tesistance (Less than 20 ohms.) between the teminals that had the red wire connected to them. I think red is one winding and black is the other winding. When the three pairs of main contacts of contactor km2 are connected, the phase sequence of the three-phase power supply is connected to the motor according to l1-la-li, and the motor rotates in the opposite direction.I don't think the way you have labled the wires as live and neutral is correct. When the three pairs of main contacts of contactor KM1 are connected, the phase sequence of the three-phase power supply is connected to the motor according to l-l2-l3. forward switching contactor KM1 and reverse switching contactor km2. Two contactors are used in the control circuit shown, i.e. When SB2 is pressed, KM is closed, the motor is rotating forward, and the normally closed contact of SB2 is also disconnected, KM cannot self lock, so the motor can rotate forward by pressing SB2, and when it is released, the motor stops rotating, thus realizing the inching control.įorward and reverse inching control circuit diagram (2) Its normally open contact is directly connected with the coil of KM, while the normally closed contact is connected with the normally open contact of KM. Since the control circuit has a self-locking, the motor will rotate forward continuously as long as this button is pressed once. Press the SB1 button, the km (contactor) coil is powered on, the normally open contact is closed, the circuit is powered on, and the motor is rotating forward. Forward and reverse inching control circuit diagram (I)
